==4.1 Properties of Materials==
Physical Properties:
- Mass
- Weight
- Volume
- Density
- Hardness
- Electrical Resistivity
- Electrical Insulator - Reduces transmission of electric charge.
- Thermal Expansion - A measure of the degree of increase in dimensions when an object is heated. This can be measured by an increase in length, area or volume. The expansivity can be measured as the fractional increase in dimension per kelvin increase in temperature.
Mechanical Properties:
- Tensile Strength - The ability of a material to withstand pulling (apart) forces.
- Compressive Strength - The ability of a material to withstand being pushed or squashed.
- Stiffness - The resistance of an elastic body to deflection by an applied force
- Toughness - The ability of a material to resist the propagation of cracks.
- Brittle - Breaks into numerous sharp shards.
- Ductility - The ability of a material to be drawn or extruded into a wire or other extended shape.
- Stress - The load on a structural member divided by its cross-sectional area is called the “stress in the member”.
- Strain - The response of a material due to stress, defined as the change in length divided by the original length.
Young’s Modulus - A measure of the stiffness of an elastic material and defined by stress/strain.
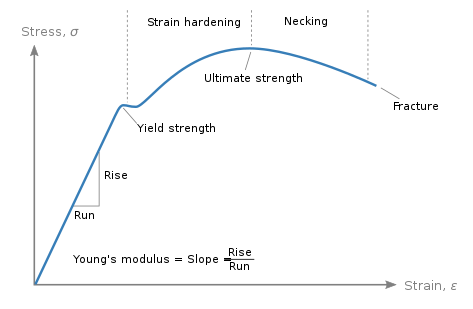
- Elasticity (Elastic region) - The extent to which a material will return to its original shape after being deformed.
- Plasticity (Plastic region) - The ability of a material to be changed in shape permanently.
Material Selection Charts - A chart used to identify appropriate materials based on the desired properties. 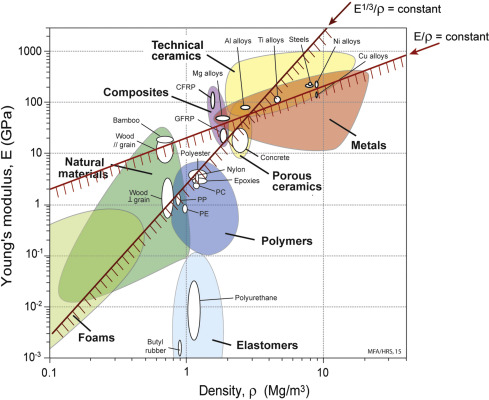
Aesthetic Characteristics:
- Aesthetic Appeal – Favourable in terms of appearance.
- Smell: the ability to perceive odours such as sweet, acrid or fragrant
- Taste: sour, sweet, spicy.
- Sound: related to pitches but also the sound of a crisp apple or a chip/crisp bag that makes a crinkling sound.
- Texture: it is how something feels or looks, it can be rough or smooth
- Appearance: the design of appearance in a product must be aesthetically pleasing to attract a customer. unless it is for a certain market.
- Colour: can be warm (e.g. browns) or cool (eg blues) can have psychological affects (e.g. greens are calming)
- Shape: geometric or organic
Properties of Smart Materials:
- Piezoelectricity - Piezoelectric materials give off a small electrical discharge when deformed. The process of using crystals to convert mechanical energy into electrical energy or vice versa
- Shape Memory - are metals that exhibit pseudo-elasticity and shape memory effect due to rearrangement of the molecules in the material.
- Photochromicity - refers to a material that can described as having a reversible change of colour when exposed to light.
- Electro-rheostatic (ER) and magneto-rheostatic (MR) - materials are fluids that can undergo dramatic changes in their viscosity.
- Thermoelectricity - is, at its simplest, electricity produced directly from heat. It involves the joining of two dissimilar conductors that, when heated, produce a direct current.
Superalloys - is an alloy that exhibits excellent mechanical strength, resistance to thermal creep deformation, good surface stability and resistance to corrosion.
Grain Size - metals are crystalline structures comprised of individual grains.
- The grain size can vary and be determined by the heat treatment.
- Reheating a solid metal or alloy allows the grains to change their structure.
- Slow cooling forms larger grains
- Rapid cooling (quench) forms smaller grains.
- Directional properties can be formed by selectively cooling one area of the solid.
- Grain size in metals can affect the properties:
- tensile strength – coarse grains the stronger a metal
- toughness – large or coarse grains the tougher the metal
- ductility – coarse grains the more ductile a metal
- brittleness – the smaller the grains the more brittle the metal
- flexibility/malleability – coarse grains the more malleable a metal
- can affect density
Alloying - alloys are a mixture that contains at least one metal.
Alloys compared to pure metals:
- Alloying increases strength and hardness
- Alloying reduces malleability and ductility, of alloys compared to pure metals.
- This is due to the presence of “foreign” atoms which interfere with the movements of atoms in the crystals during plastic deformation
Work hardening (Cold working or Strain Hardening) - is the process of toughening the a metal through plastic deformation.
Tempering - Tempering is a heat treatment process
Two criteria for super alloys are creep and oxidation resistance:
Creep
- Creep is the tendency of a metal (or material) to slowly move or deform permanently due to the long term exposure of stress that are below the yield strength or ultimate strength of the metal. Creep is more severe when metals are subjected to near the melting point heat for long periods of time. (Wikipeadia 2007)
Oxidation resistance
- Oxidation is the interaction between oxygen and different substances when they make contact, such as rust Fe2O3
- Oxidation resistance is the ability of a material to resist the direct and indirect attack of oxygen (oxidation) and degradation.
Recovery and disposal
Of metals and metallic alloys
- Metals and metallic alloys are so widely used.
- They are easily recyclable
- They can be indefinitely recycled
- It can reduce the emissions and the affect on the environment
- Reduce energy required to produce new metal
Ferrous Alloys - contain iron (makes them magnetic). Non-ferrous contains no iron:
- Mild Steel
- Stainless Steel
- Cast Iron
Non-ferrous Alloys
- Aluminium
- Copper
- Brass
- Silver
- Lead
==4.2 Timber==
- Natural timber is a natural composite material comprising cellulose fibres in a lignin matrix
Moisture content of natural timber
- Absorbed moisture is the moisture contained in the cell walls of timber.
- Free moisture is the moisture contained within the cell cavities and intercellular spaces.
- Equilibrium Moisture content (EMC): This is when the moisture content of wood is at equilibrium (same as) the local environment. This can be affected by humidity and temperature changes.
Seasoning - Seasoning is the commercial drying of timber which reduces the moisture content of wood:
- Kiln seasoning - is carried out in a thermally insulated chamber, a type of oven, that produce the appropriate temperatures to complete the processes, such as hardening, drying, or chemical changes.
- Air-drying - Air- drying are stacks of sawn timber in the open or in large sheds. There is little control over the drying process as the weather elements have affects.
- Kiln-drying - are stacks of sawn timber in a kiln, to reduce the moisture content in wood, where the heat, air circulation, and humidity is closely controlled.
Timber Defects:
- Warping is the distortion in wood caused by uneven drying, which results in the material bending or twisting.
- Bowing is the warping along the length of the face of the wood.
- Cupping is the warping across the width of the face of wood, in which the edges are higher or lower than the centre.
- Twisting is the warping where the two ends of a material do not lie on the same plane.
- Knots are imperfections in timber, caused by the growth of branches in the tree that reduces its strength.
Hardwood trees *The wood from a deciduous (broadleaved) tree.*includes eucalyptus, elm, maple, oak, and beech. | Softwood trees *The wood from a coniferous (evergreen) tree.*includes are pine, cedar, and cypress |
---|
Characteristics of natural timber
- Tensile Strength - The tensile strength of natural timber is greater along the grain than across the grain.
- Resistance to damp environments: is very resistant.
- Longevity - Hardwoods very good. Softwoods good.
- Aesthetic properties - natural colours range (red, purple, cream and brown). The grain can add to its aesthetics.
Man-made timbers - Also known as Engineered board or composite wood
- Man-made timber include:
- Plywood (Laminated boards) are layers of veneers (very thin slices of wood) glued together perpendicularly.
- Particle board (Chipboard) which is made from different sizes of wood chips, joined with glue and pressed.
- MDF (Medium Density Fibre Board) strands of fibre ruled together and pressed into sheets.
Characteristics of man-made timber
- Tensile strength: depends on the man-made timber
- Plywood – high tensile strength in all directions
- Particle board and MDF – very low
- Resistance to damp environments: depends on the man-made timber.
- Exterior plywood – excellent.
- Interior plywoods very low
- Particle board and MDF – very low
- Longevity:
- Plywood is high
- Particle board and MDF is low to medium
- Aesthetic properties:
- Plywood if the top layer is of a nice timber like Beech will be good
- Particle board and MDF requires finishing or a sheet of lamination (see previous section)
Treating and finishing timbers
- Reducing attack by insects, fungus and marine borers by making the wood poisonous
- Creosote: A material that penetrates the timber fibres protecting the integrity of the wood from attack from borer, wood lice and fungal attack.
- Protection from the weather
- Protection from Dry rot.
- Where timber is subjected to decay and attack by fungus.
- Improving chemical resistance
- Enhancing aesthetic properties
- Modifying other properties
==4.2 Glass==
Characteristics of glass
Transparency
Colour
Strength – low tensile strength but high compressive strength
Brittleness - it has a low impact strength and thus will shatter easily (low toughness).
Hardness - high hardness and wont scratch readily.
Un-reactivity – is chemically inert so leaching of acid based contents is not a problem.
Non-Toxic – due to its un-reactivity therefore suitable for food storage.
Non-porous - thus will hold liquids or stop moisture seeping from outside.
Insulator.
100% recyclable and is continuously recyclable
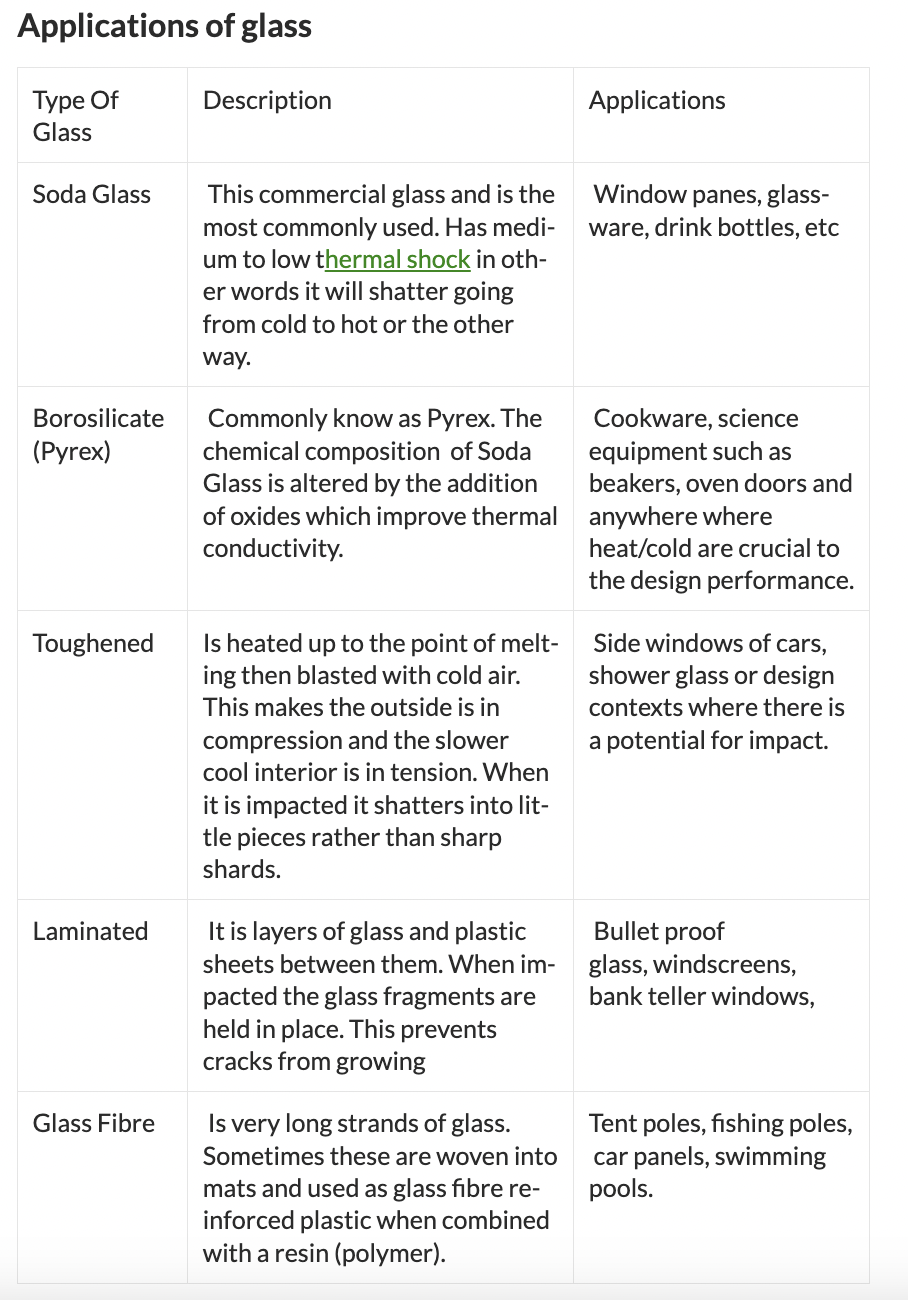
Recovery and disposal of glass
- Recycled glass is known as cullet which is added to new raw materials to make new glass.
- It reduces the energy required thus the costs in producing new glass.
- When recycled the glass is separated into the same colours groups (due to chemical compounds) then are crushed .
- Improves environmental concerns such as the extraction of raw materials, energy consumption, and reduced pollution.
- It is continuously recyclable
==4.2 Plastics==
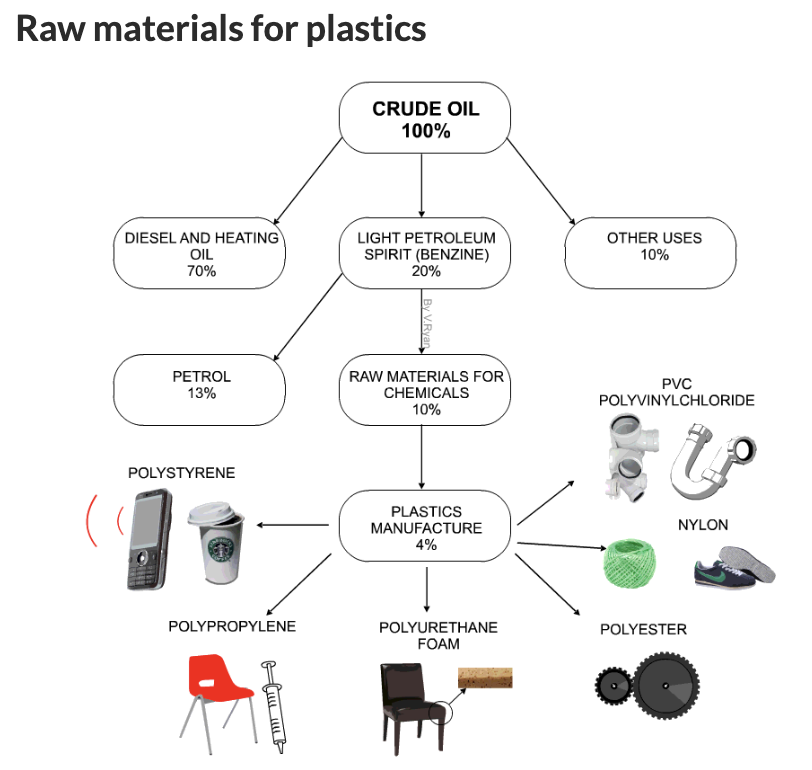
- Technically plastics are referred to as Polymers
- Petro-chemicals are the main ingredient for modern day plastics.
- Roughly 8% of oil production is due in plastics
- The raw material for plastics (mainly oil) is extracted in a country, exported to other countries where conversion to plastics takes place and these are re-exported at considerable added value. (Int Mind)
- Bio-plastics – such as polylactic acid (PLA) resin which is made from corn or potato starch – is also biodegradable.
- Interesting note on compostability of PLA
Structure of thermoplastics
Thermoplastics are linear chain molecules with weak secondary bonds between the chains.
The Making of the Modern World has an informative article on Polymers and intermolecular bonds
Tecnoelpalo on Plastics including their uses.
General characteristics include:
- ductile
- low stiffness – squishy water bottles for example
- easily injected into a mould
- can be reshaped after heating
- easily and cost effectively manufactured
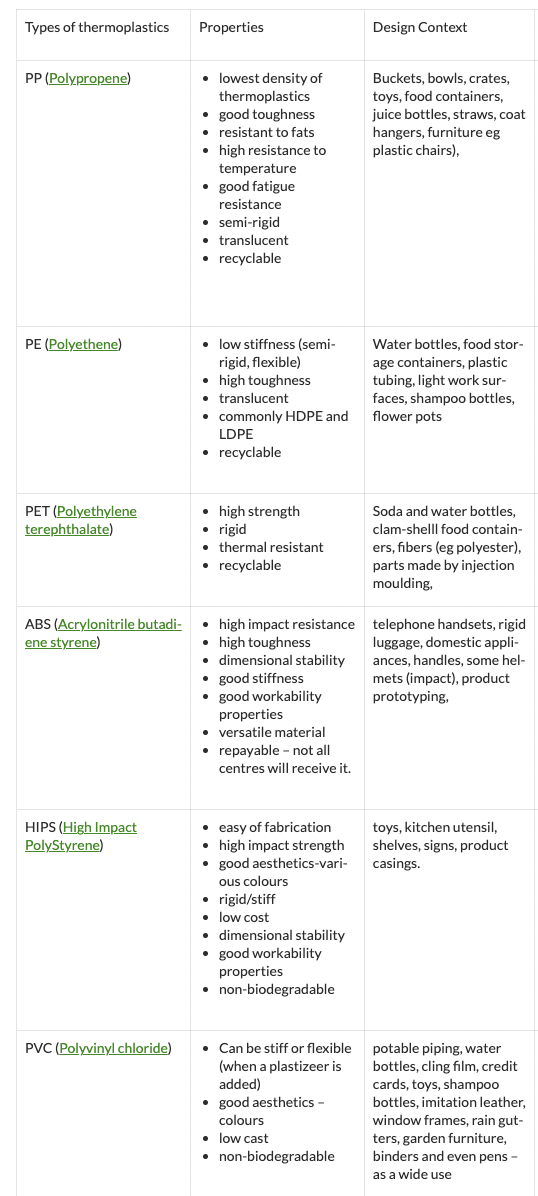
Structure of thermosetting plastics
Recovery and Disposal of Plastics:
- Nearly all plastics can be recycled it mostly depends on economic, technical and logistical factors
- Thermoplastics can be easily recycled.
- come in a range of chemical compounds and therefore need to be sorted for recycling
- Thermosets not so easy (and expensive to do so)
- need to be ground into a powder which adds time and costs.
- Often get sent to landfill
- Some plastics are not accepted at the recycling plant due to its chemical compound and the facilities capabilities.
Temperature and recycling thermoplastics:
- The Increase in temperature causes the weak secondary bonds to break (The heat is sufficient enough to break the secondary bonds but not the primary, covalent, bonds) see above image.
- This allows the long molecular chains to slide over each other, i.e. be reshaped into a new product.
- When a plastically deformed and allowed to cool it will remain in the new shape due to new secondary bonds being formed.
- The nature of the structure of a thermoplastic allows it to be readily recycled.
==4.2 Textiles==
Natural Fibers:
Properties:
- Absorbency – is very high
- Strength – low tensile strength
- Elasticity – not very elastic
- Effect of temperature – will burn but does not melt.
Synthetic Fibers - Fibres made from a man-made material that are spun into a thread; the joining of monomers into polymers by the process of polymerisation:
- Acrylic
- Nylon
- Polyester
- Lyrca
- Rayon
- Acetate
- Spandex
- Kevlar
Properties:
- Absorbency – is very low
- Strength – high tensile strength
- Elasticity – highly elastic (like stockings, socks etc)
- Effect of temperature – will burn and melt.
Weaving - The act of forming a sheet like material by interlacing long threads passing in one direction with others at a right angle to them.
Knitting - A method for converting a yarn into fabric by creating consecutive rows of interlocking loops of yarn.
Lacemaking - A method for creating a decorative fabric that is woven into symmetrical patterns and figures.
Felting - A method for converting yarn into fabric by matting the fibres together.
Design contexts:
Wool
- Clothing – sweaters/jumpers, suits, socks, etc
- Upholstery – couches, chairs etc
- Rugs
- Blankets
- Industrial use – padding, structural insulation, mattresses & futons, oil & hazardous liquids clean up pads, …
Cotton
- Clothing – pants, underwear, T-shirts, etc
- Bedding/furnishings – sheets, covers, pillows …
- Industrial use – wall coverings, book binding tapes, tarpaulins, threads for sewing …
Silk
- Clothing – shirts, under garments, pyjamas, robes …
- Medical sutures (stitches)
- Upholstery & Bedding
Nylon
- Clothing – raincoats, stockings, socks …
- Industrial use – parachutes, tents, tyres, ropes …
Polyester
- Industrial use – seat belts, tents, transportation upholstery, ropes, sails, fish nets,
- Clothing – underwear, night wear and high pile fabrics.
- Furnishings – curtains, drapes, upholstery, carpets and rugs
Lyrca
- Close fitting clothing.
- Sportswear – cycling, running, etc
- Underwear
==4.2 Composites==
Composite - a material which is produced from two or more constituent materials
Composition and structure of composites:
- Concrete
- Engineered wood – also called composite wood, man-made wood, or manufactured board. gluing sheets (veneer), particles or stands of wood together.
- Plywood – sheets of venner glued together with the grain perpendicular to each sheet.
- Particleboard – chips of wood glued together
- Fibreglass – stands of glass, formed into a matt and then covered in resin (polymer/thermoset plastic).
- Carbon- reinforced plastic – carbon fibres formed into a matt (see above image) then covered in resin.
- Laminated veneer lumber (LVL) – uses multiple layers of thin wood assembled with adhesives
==4.3 Scale of Production==
Craft production – A small-scale production process centred on manual skills.
Mechanized production – A volume production process involving machines controlled by humans.
Automated Production – A volume production process involving machines controlled by production computers
One-off Productions - an individual product or a prototype for larger-scale production.
%%Advantages%%
- Highly customisable to consumers needs.
- Flexibility for the designer and consumer.
- Allow for testing of prototypes before continuous flow production.
==Disadvantages==
- Can be expensive as any tools or machinery needed are included in the final cost.
- Time consuming if craft manufacturing techniques are used
- May be that the product is not designed for disassembly (DfD) there are no interchangeable parts.
Batch Production - it is a limited production run (a set number of items to be produced).
%%Advantages%%
- Cheaper than one-off production
- Customisable products but not as highly as one-off production.
- Easily adjust to market demands or seasonal items
- Greater consumer choice (e.g. Swatch watches).
- For smaller or upstart companies that can’t afford continuous flow production.
- It can reduce initial capital outlay because a single production line can be used to produce several products.
==Disadvantages==
- Down time between productions runs when retooling.
- Products have to be stored raising the costs per item.
Mass Production - The production of large amounts of standardized products on production lines, permitting very high rates of production per worker.
Continuous Flow Production - Continuous flow is a production method used to manufacture, produce or process materials without interruption.
%%Advantages%%
- Cheaper than other production methods (economies of scale).
- If a part or product needs replacing consumer is assured that it still exists (e.g. bic pens).
- Lack of inventory which reduces storage costs.
==Disadvantages==
- Standard products so less choice for the consumer.
- Automated production is high in initial costs
- Training of staff to run machines and CIM
Mass customisation - A CIM system that manufactures products to individual customer needs or wants.
%%Advantages%%
- Economies of scale are achieved even for small orders
- Highly customisable to consumer needs or likes
==Disadvantages==
- Long layover time from with product is customised to reaching the consumer.
- Very high initial capital costs
- Special training for employees
Manufacturers choose a scale of production for various reasons
- Product characteristics – complexity, features, design, product family, etc
- Staff skills – high tech skills for automation.
- Financial Considerations – is it cost effective to produce, profits, etc
- Material characteristics – plastics are suited to continuos flow production more than say certain metals or other materials.
- Size of market – Mont Blanc pens are geared to a market segment which is small whereas Bic pens target are wider market for cheap disposable pens.
- Nature of market – such as the variety of products expected by the consumer such as Swatch watches.
- Desired manufacturing processes – injection moulding is suited to continuos flow production because it an be fully automated and use cheap thermoplastics
- Desired production scale – such as one-off, batch or continuos.
==4.4 Manufacturing Process==
Design for manufacture (DfM) – Designers design specifically for optimum use of existing manufacturing capability.
Additive Techniques - Are manufacturing techniques that add material in order to create a product or component.
Paper based rapid prototyping - is a process where design teams create paper representations of digital products to help them realize concepts and test designs.
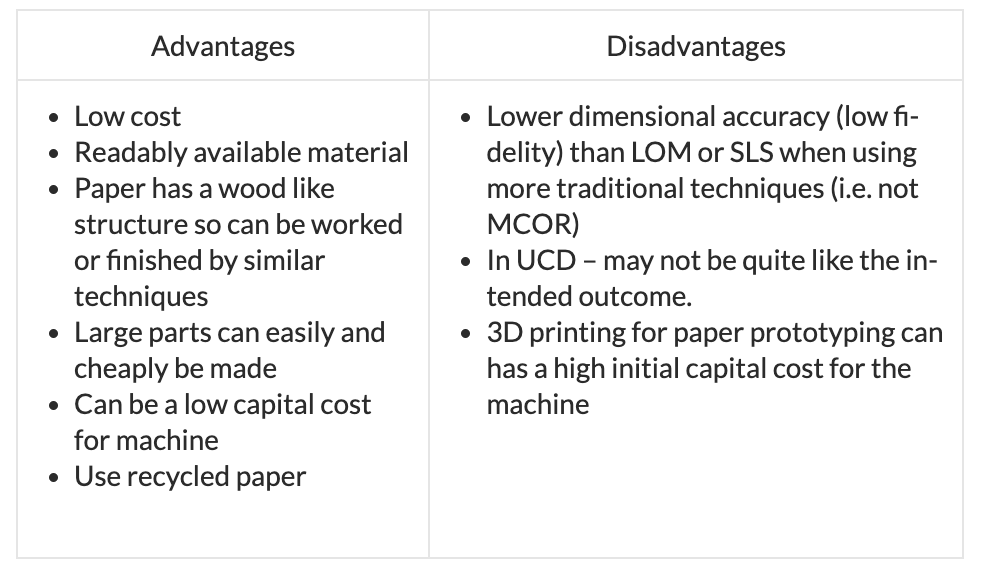
Laminated object manufacture (LOM) - A rapid prototyping systems that creates a 3D product by manufacture (LOM) converting it into slices, cutting the slices out and joining/gluing the slices together
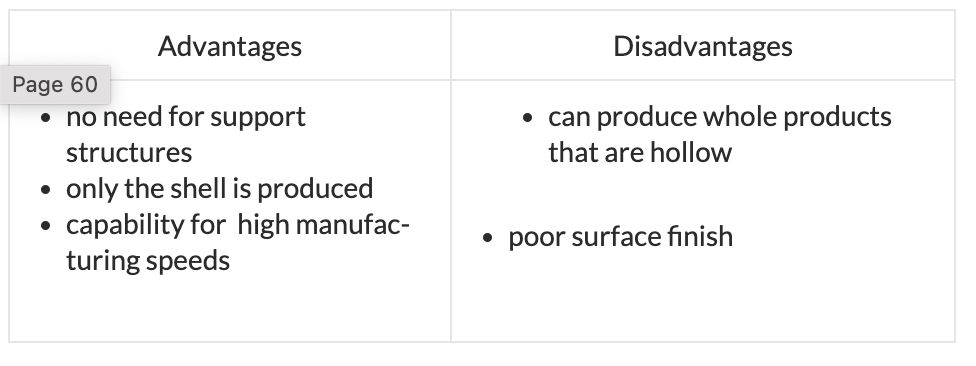
Stereolithography (SLA) - is an industrial 3D printing process used to create concept models, cosmetic prototypes, and complex parts with intricate geometries in as fast as 1 day.
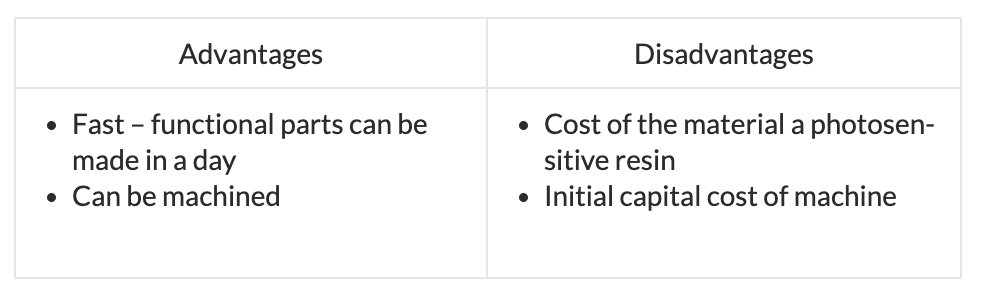
Subtractive/Wasting Techniques - Are manufacturing techniques that cut away material in order to create a product or component
Cutting - Is where a material is reduced into he desired shape through sitting away material
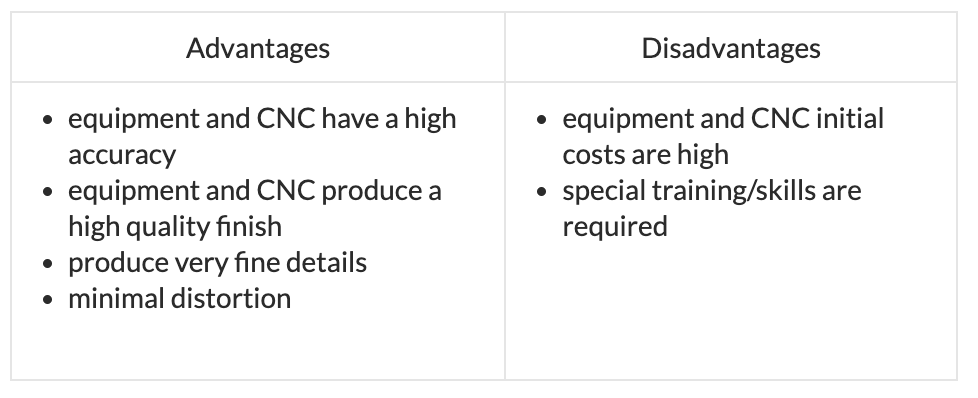
Machining - Is the removal of material by a tool that moves across the material by use a machine or large equipment
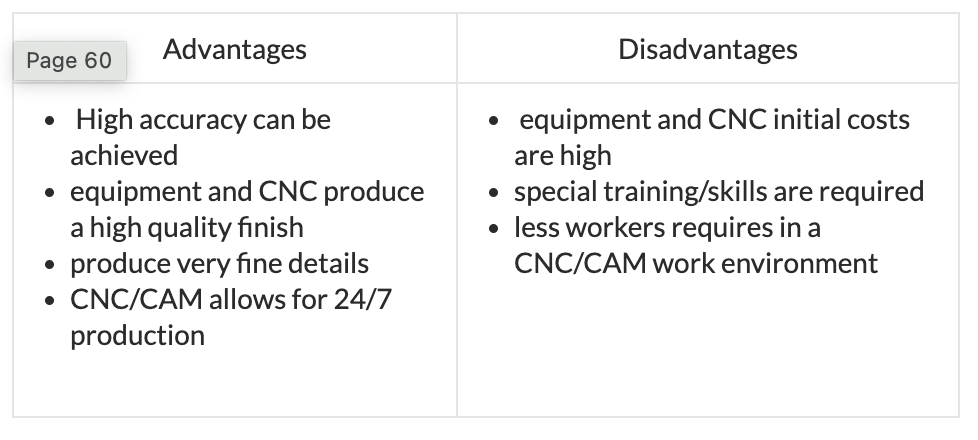
Turning - The material is held between two centres and the tool moves longitudinally across it removing material.
Milling - The material is held firm in a vice on a movable bed and a rotating cutting tool sweeps along the paths on the surface of the material. The bed moves the material around while the cutting moves only through the z-axis.
Drilling - Is boring a hole into a piece of material. The Material is held firm and does not move and a rotating drill bit moves through the z-axis removing material.
Abrading - Wearing away material using abrasive material. (sand or abrasive paper, scapers)
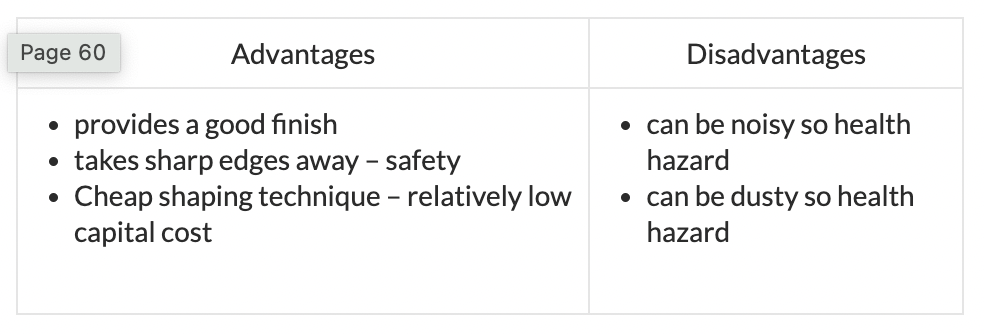
Shaping techniques - Are manufacturing methods for modifying the shape of a material.
- Moulding - Heat a material until it is a liquid or pliable state. Then placing into a mould. Materials used: usually plastic/polymer but can be glass or metal.
- Injection moulding
- Blow moulding - Is the process of inflating a hot, hollow, thermoplastic that is inside a closed mould. A blast of hot air is sent in which expands the plastic so it conforms which the mould cavity.
- Rotational moulding - Heated hollow mould is rotated during the heating up of the plastic and cooling.
- Compression moulding - Where the material is heated so it is pliable. It is placed in an open mould that closes and compresses the material to the shape of the mould cavity.
Thermoforming - Where a plastic sheet is heated until it is in a pliable state. Then placing into a mould to form a shape. Vacuum forming is a common method used.
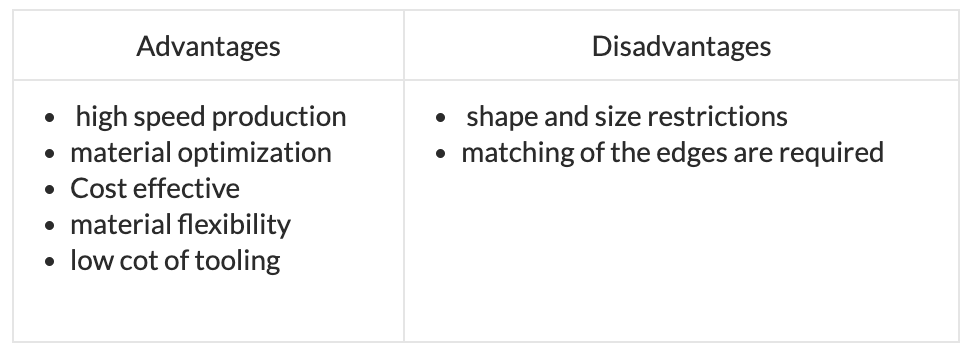
Laminating - sheets of thin veneer (about 1 mm thick) are layered with a glue (polymer) in-between. Materials used: glass, timber, paper and plastic.
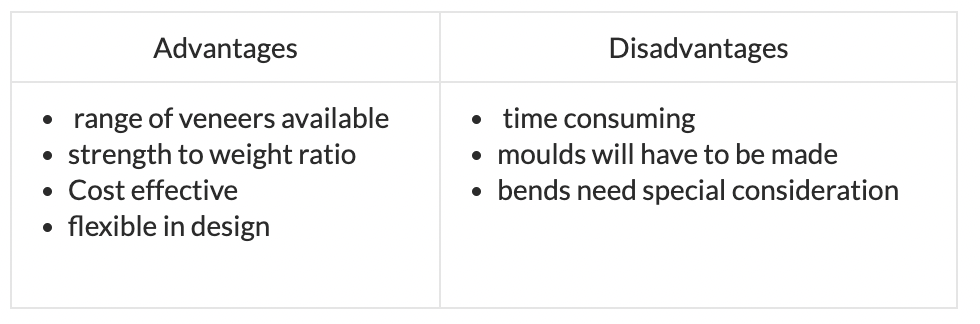
Casting - Pouring a molten material (metal) into a mould. Often the mould is broken. The shape is called a casting. Materials used: metals.
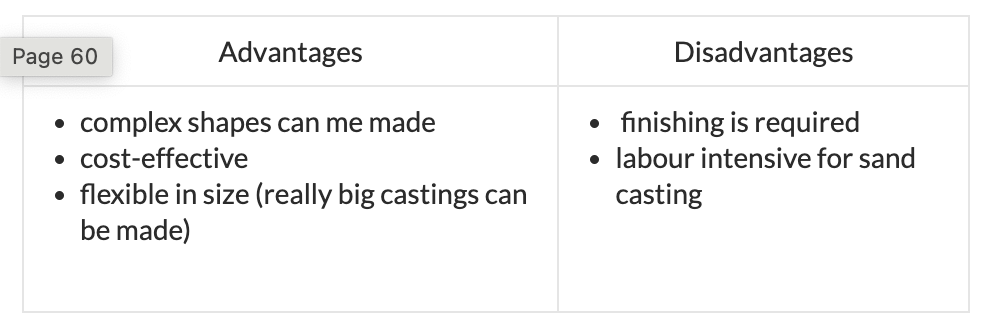
Knitting
Weaving - is an ancient textile art and craft that involves placing two sets of threads or yarn called the warp and weft of the loom and turning them into cloth. In general, weaving involves the interlacing of two sets of threads at right angles to each other: the warp and the weft.
Joining techniques - Methods that are used to join two similar or dissimilar materials together.
Permanent:
Adhering (or Gluing)
Fusing
Fasteners (Permanent )
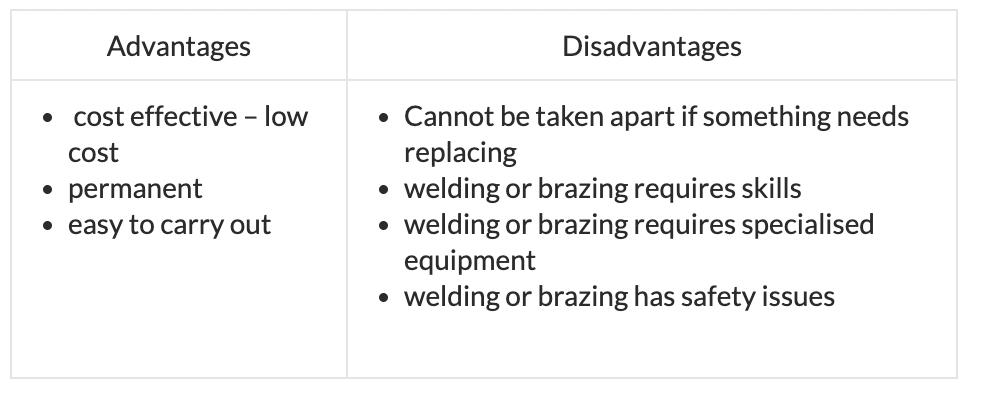
Temporary:
- Fasteners (Temporary) - The use of fasteners stands for using certain connecting devices to join two or more dissimilar materials together. They can be undone to separate the materials if needed.
- Adhering - Thermoplastic glue such as that used in hot glue guns
==4.5 Production Systems==
Craft production - A production process that based on manual skills. It is a small-scale production.
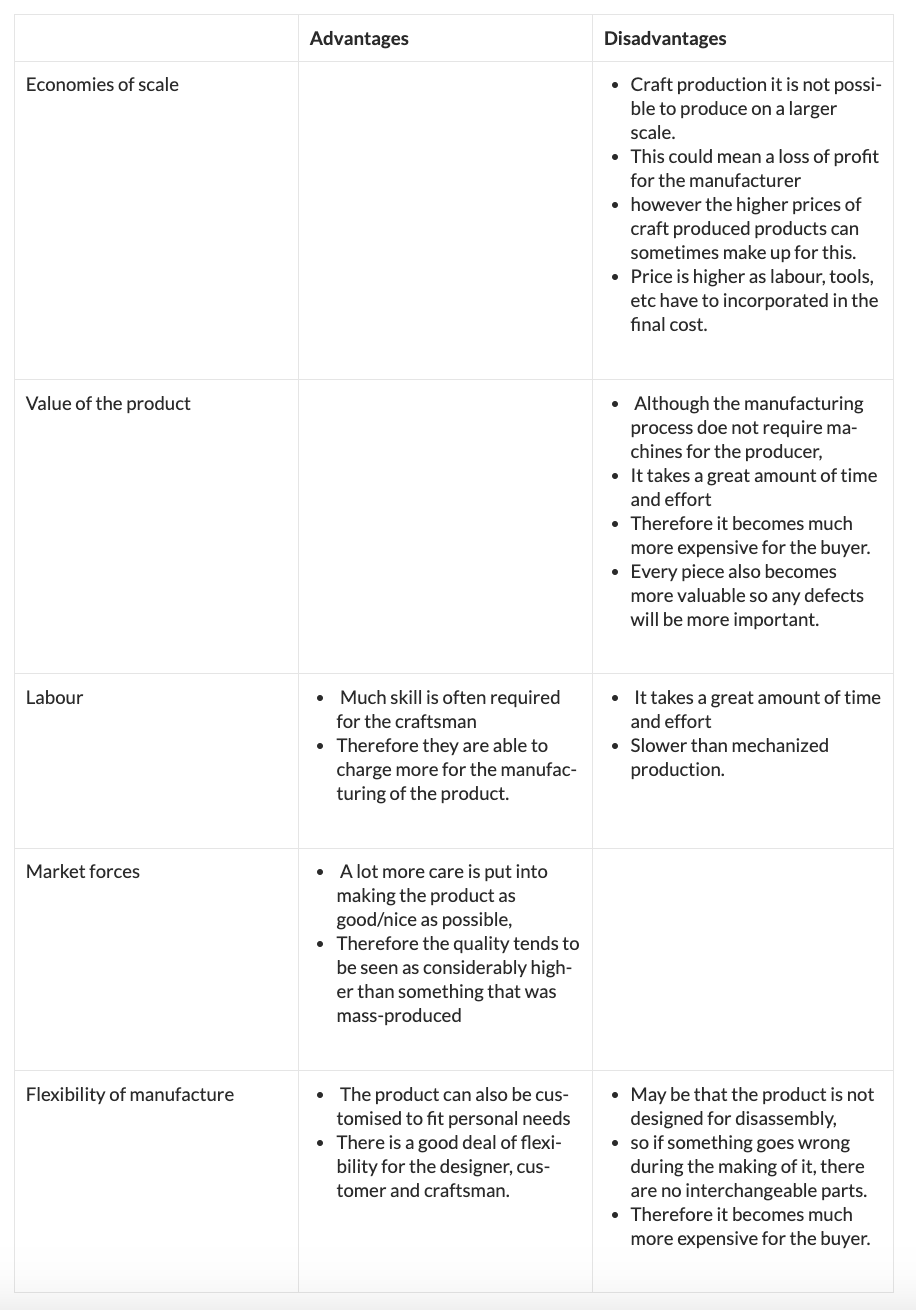
Mechanized production - A volume production process where machines are controlled by humans.
Automated production - A volume production process involving machines controlled by computers.
Computer numerical control (CNC) - refers to the computer control of machines for the purpose of manufacturing complex parts in metals and other materials. Machines are controlled by a programme commonly called a “G code”. Each code is assigned to a particular operation or process. The codes control X, Y and Z movement and feed speeds.
==4.6 Robots in Automated Production==
Work envelope - The 3D space a robot can operate within, considering clearance and reach
Load capacity - Within this context, the weight a robot can manipulate.
Single-task robots – can only carry out one task at a time
Multi-task robots – can carry out more than one task at a time
Teams of robots – groups of robots carry out similar tasks
Machine to machine (M2M) – where wireless and wired systems communicate between devices to share information or send instructions.
%%Advantages of using robotic systems in production:%%
- Improve health and safety of workforce.
- High accuracy of work – reduced errors and waste ($). Quality of final product is up.
- Perform repetitive and dangerous tasks
- Work in confined spaces.
- Perform functions 24/7 leading to higher production
- Reprogrammability or flexible
==Disadvantages of using robotic systems in production:==
- Expertise needed to operate such systems.
- Training of workers required in both operation and maintenance.
- High initial capital cost+
Robot generations:
- First-generation robots - are a simple mechanical arm that has the ability to make precise motions at high speed. They need constant supervision by a human operator.
- Second-generation robots - are equipped with sensors that can provide information about their surroundings. They can synchronize with each other and do not require constant supervision by a human; however, they are controlled by an external control unit.
- Third-generation robots$$ - are autonomous and can operate largely without supervision from a human. They have their own central control unit. Swarms of smaller autonomous robots also fit in this category.